CornerTurn, LLC was awarded a Seaport-e prime contract on 13 August 2012 with approval to respond to solicitations for Zone 2 and Zone 6.
Services Experience
Cornerturn, LLC. provides capabilities in the following functional areas as defined in the Seaport-e contract:
3.1 Research and Development Support
3.2 Engineering, System Engineering and Process Engineering Support
3.3 Modeling, Simulation, Stimulation and Analysis Support
3.4 Prototyping, Pre-Production, Model-Making and Fabrication Support
3.6 Software Engineering, Development, Programming and Network Support
3.14 Interoperability, Test and Evaluation, Trials Support
Previous Experience
Quality Assurance Program
The basic philosophy of ISO 9001 is to define the procedures your company will follow to consistently develop and deliver high quality products and services. It consists of creating an overall Quality Management System that defines procedures for Management Responsibility, Resource Management, Product Realization, and Measurement, Analysis and Improvement that provides a basic infrastructure and company culture for developing and delivering products. The high level interactions between these “functions” are illustrated in Figure 1 below.
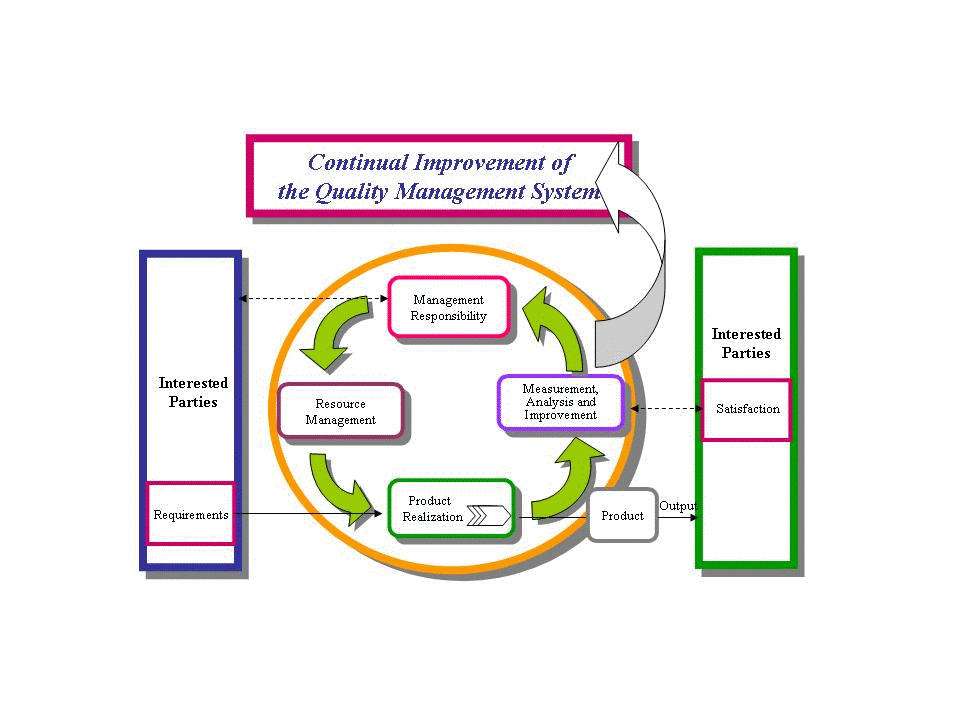
Figure 1. Conceptual Quality Management System
CornerTurn has defined their Management Responsibility as follows:
- Make a top level commitment to creating a Quality Management System
- Define all company procedures with a focus on customer satisfaction
- Define a Quality Policy for the company
- Develop Quality Objectives that are meaningful and support monitoring of the company performance to identify areas where improvement is needed
- Identify and assign specific responsibilities and authority to company individuals and define effective communication methods to support the Quality Policy
- Regularly review the Quality Management System and make modifications as needed
The Resource Management portion of the system accounts for:
- Provide the necessary resources (manpower, materials and time) to support the QMS
- Provide adequate personnel Training
- Provide and maintain the required infrastructure (this includes buildings, workspace, workstations, and development tools (both HW and SW))
- Create and maintain a healthy and effective work environment; this includes the physical aspects of the work environment as well as developing a culture of respect, tolerance, team support and open-mindedness among the employees.
The Product Realization and Measurements portion of the system includes:
- Define a methodology for planning the overall Product Realization strategy
- Identify methods for determining and reviewing the requirements for each product, and develop methods for communicating with each customer to confirm that the complete set of product requirements has been assembled.
- Define procedures for all aspects of Design and Development; this includes Planning, defining Inputs and Outputs, setting up Review Procedures, defining product Verification and Validation techniques, and developing procedures and tools to changes in the product design at all stages of the development cycle.
- Create guidelines for Purchasing products from other suppliers.
- Define the overall methodology for providing Products and Services in a repeatable, efficient manner.
- Define techniques for controlling and maintaining any measuring and monitoring equipment used to test or inspect products being developed.
CornerTurn Management has created a complete Quality Management System as described above and has achieved ISO 9001 certification.